![]() |
Xiamen Bioleader Environmental Protection Co., LtdProfessional Supplier of Biodegradable Tableware and Food Packaging! |
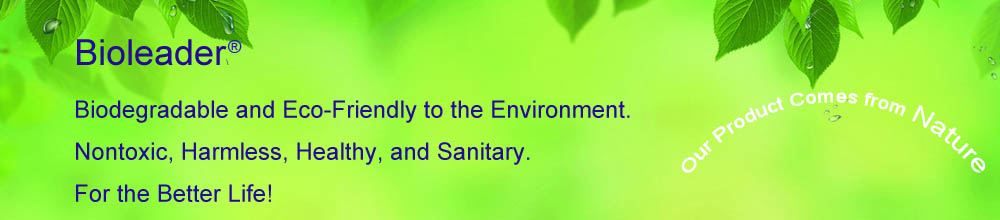
Bioelectricity versus bioethanol from sugarcane bagasse: is it worth being flexible?
Background
Sugarcane is the most efficient crop for production of (1G) ethanol. Additionally, sugarcane bagasse can be used to produce (2G) ethanol. However, the manufacture of 2G ethanol in large scale is not a consolidated process yet. Thus, a detailed economic analysis, based on consistent simulations of the process, is worthwhile. Moreover, both ethanol and electric energy markets have been extremely volatile in Brazil, which suggests that a flexible biorefinery, able to switch between 2G ethanol and electric energy production, could be an option to absorb fluctuations in relative prices. Simulations of three cases were run using the software EMSO: production of 1G ethanol + electric energy, of 1G + 2G ethanol and a flexible biorefinery. Bagasse for 2G ethanol was pretreated with a weak acid solution, followed by enzymatic hydrolysis, while 50% of sugarcane trash (mostly leaves) was used as surplus fuel.
Results
With maximum diversion of bagasse to 2G ethanol (74% of the total), an increase of 25.8% in ethanol production (reaching 115.2 L/tonne of sugarcane) was achieved. An increase of 21.1% in the current ethanol price would be enough to make all three biorefineries economically viable (11.5% for the 1G + 2G dedicated biorefinery). For 2012 prices, the flexible biorefinery presented a lower Internal Rate of Return (IRR) than the 1G + 2G dedicated biorefinery. The impact of electric energy prices (auction and spot market) and of enzyme costs on the IRR was not as significant as it would be expected.
Conclusions
For current market prices in Brazil, not even production of 1G bioethanol is economically feasible. However, the 1G + 2G dedicated biorefinery is closer to feasibility than the conventional 1G + electric energy industrial plant. Besides, the IRR of the 1G + 2G biorefinery is more sensitive with respect to the price of ethanol, and an increase of 11.5% in this value would be enough to achieve feasibility. The ability of the flexible biorefinery to take advantage of seasonal fluctuations does not make up for its higher investment cost, in the present scenario.
Keywords
Second generation ethanol production Techno-economic evaluation Lignocellulose Sugarcane Bagasse Process simulationBackground
It is already a consensus that a shift of the global energy matrix towards renewable sources is mandatory. Yet, the role that each specific alternative will play, say, at the year 2050, will be defined along the road, depending on technological developments, political options by stakeholders, economical and social demands. Anyway, in this scenario ethanol will certainly be an important biofuel.
Sugarcane is known to be the most efficient crop for 1G ethanol production, with an energy balance of 9.3 produced/consumed tonne of oil equivalent (toe) [1]. During the 1970’s the Brazilian government initiated the National Ethanol Program (PROALCOOL, in Portuguese, [2]) to decrease national dependence on oil. Since then, the use of 1G ethanol as a vehicle fuel has been consolidated, and presently 86% of the cars sold in this country are flex-fuel, running with any mixture of ethanol and gasoline [3]. In modern facilities, ethanol production is a highly integrated process, with sugarcane bagasse burnt in boilers to supply the industrial plant energy demands, further exporting the surplus of electric energy to the grid.
One of the alternatives for the industrial production of 2G ethanol is the biochemical route, i.e., acid or enzymatic hydrolysis of the biomass followed by fermentation of the resulting sugars. Logistics and transportation of the lignocellulosic raw material may be a bottleneck for 2G ethanol [4]. From this point of view, sugarcane bagasse has an important advantage, since it has already been collected and processed for the extraction of the juice, being immediately available at the plant site. Moreover, sugarcane trash (mostly the leaves) can be transported with the stalk, after small adaptations of the mechanical harvesting – although part of this biomass must be left for covering the fields [5]. Since the process must be energetically self-sufficient, the addition of sugarcane trash as boiler fuel can increase the amount of bagasse available for hydrolysis, therefore enhancing ethanol yields.
Industrial production of 2G ethanol is still not consolidated in large scale. Therefore, an economic analysis is important to indicate if it is the most interesting alternative, specially when compared to selling electric energy (bioelectricity). Nevertheless, this answer is not unique, given the volatility of relative prices: biomass electricity prices in public auctions in Brazil ranged from 85.35 USD/MWh to 53.02 USD/MWh in the last two auctions (Aug/2010 and Aug/2011) [6], a -37.9% variation. The spot market (that buys surplus power, beyond the amount contracted during the auctions) presented an even higher range of prices, between 3.26 USD/MWh and 341.13 USD/MWh over the last nine years (Jan/2003 - Dez/2012) [7]. Ethanol prices are equally volatile, changing from 0.258 USD/L to 0.818 USD/L (for the hydrated fuel) over the same period of nine years [8]. All prices above, used in this study, were calculated in Brazilian reais, brought to December/2012 value (to take into account the inflation in the period), and converted to US dollars using the exchange rate value of 2.077 BRL/USD (dez/2012).
Sugarcane biorefineries have been intensively studied by the recent literature. Seabra et al. (2011) [9] presented economic and environmental analyses of a sugarcane biorefinery. The authors concluded that, although electric energy presented a better economic feasibility, its environmental impact was greater than the one for second generation ethanol. An economic analysis comparing 2G ethanol production with electric energy was also done by Dias et al. (2011) [10]. The authors concluded that, although for the present technology electric energy is a better option, 2G ethanol can compete with it if sugarcane trash is used, provided that new technologies could increase yields. On the other hand, Macrelli et al. (2012) [11] presented results for several sugarcane biorefineries configurations and concluded that 2G ethanol from sugarcane is already competitive with 1G starch-based ethanol in Europe. The advantages of the integrated production of 1G and 2G ethanol production based on sugarcane was highlighted by Dias et al. (2012) [12]. The integrated biorefinery presented higher ethanol production rates, and better economic and environmental performance, when compared to a stand-alone 2G ethanol-from-sugarcane bagasse plant.
The 2G biorefinery could be flexible, just as the industry that employs current 1G technology already is, shifting between sugar and ethanol production. This new flexible biorefinery might be able to choose between electric energy and 2G ethanol production. The present study focuses on assessing the economic feasibility of a flexible biorefinery, for an autonomous distillery (not considering the manufacture of sugar), and comparing it to the dedicated 1G + electric energy and 1G + 2G ethanol biorefineries. The process chosen as case study uses enzymatic hydrolysis of the biomass (sugarcane bagasse) and ethanolic fermentation of hexoses and pentoses. Specifically, this study presents a computational applicative that may be a useful tool for the process scheduling of future cane-based biorefineries but, beyond that scope, that may also support decision-making concerning national energy policies. Such computationally robust tool was developed within an equation-oriented simulator (EMSO) [13] and is based on phenomenological modelling, at least for the most important unit operations and reactors that are present in the process.
Results and discussion
Process simulation

Process diagram for first generation ethanol production.

Process diagram for second generation ethanol production.
Main streams for 1G + Cogeneration biorefinery (BioEE)
Stream n° |
Mass flow (kg/h) |
Temperature (°C) |
Pressure (bar) |
Fraction of sugars |
---|---|---|---|---|
1 |
500000 |
30 |
1 |
0.145 |
2 |
495675 |
30 |
1 |
0.144 |
3 |
131791 |
30 |
1 |
0.02 |
4 |
512584 |
30 |
1 |
0.134 |
5 |
513565 |
90 |
1 |
0.133 |
6 |
389697 |
111.7 |
1 |
0.177 |
7 |
578699 |
31 |
1 |
0 |
8 |
90016 |
31 |
1 |
0 |
9 |
189003 |
30 |
1 |
0 |
10 |
488683 |
31 |
1 |
0 |
11 |
299182 |
110.5 |
2.5 |
0 |
12 |
293196 |
189.3 |
2.5 |
0 |
13 |
193026 |
55.7 |
0.1 |
0 |
Main streams for 1G + 2G biorefinery (BioEth)
Stream n° |
Mass flow (kg/h) |
Temperature (°C) |
Pressure (bar) |
Fraction of sugars |
---|---|---|---|---|
1 |
500000 |
30 |
1 |
0.145 |
2 |
495675 |
30 |
1 |
0.144 |
3 |
131791 |
30 |
1 |
0.02 |
4 |
512584 |
30 |
1 |
0.134 |
5 |
513565 |
90 |
1 |
0.133 |
6 |
332396 |
111.7 |
1 |
0.206 |
7 |
493607 |
31 |
1 |
0 |
8 |
76920.5 |
31 |
1 |
0 |
9 |
161212 |
30 |
1 |
0 |
10 |
416687 |
31 |
1 |
0 |
11 |
196577 |
110.5 |
2.5 |
0 |
12 |
188785 |
189.3 |
2.5 |
0 |
13 |
0 |
55.7 |
0.1 |
0 |
14 |
97613.3 |
30 |
1 |
0.02 |
15 |
174018 |
30 |
1 |
0 |
16 |
271631 |
120 |
2 |
0.02 |
17 |
201087 |
100 |
1 |
0.02 |
18 |
70544 |
100 |
1 |
0.01 |
19 |
201045 |
27 |
1 |
0.02 |
20 |
153036 |
50 |
1 |
0.02 |
21 |
153036 |
50 |
1 |
0.08 |
22 |
104925 |
50 |
1 |
0.09 |
23 |
48111 |
50 |
1 |
0.05 |
First and second generation ethanol production rates
BioEE |
BioEth |
|
---|---|---|
Ethanol production (L/h) |
45796.6 |
57580.8 |
Specific ethanol production (1G + 2G) |
91.6 |
115.2 |
(L/tonne of sugarcane (TC)) |
||
2G ethanol production (L/h) |
0 |
11784.2 |
Specific 2G ethanol production |
0 |
120.7 |
(L/tonne of bagasse (TB)) |
Steam consumption (total and specific)
Sector |
Steam consumption (total (kg/h) / specific (kg/TC)) |
|
---|---|---|
BioEE |
BioEth |
|
Juice treatment |
51971/103.9 a |
51971/103.9 a |
Concentration |
185240/370.5 |
241210/482.6 |
Distillation |
121775/243.5 a |
188455/376.9 b |
Pretreatment* |
0 |
38493/394.3 |
Total |
185240/370.5 |
289550/579.1 |
Power consumption divided by sector (positive values for produced energy and negative for consumed)
Sector |
Power demand/production (kW) |
|
---|---|---|
BioEE |
BioEth |
|
Mills |
-6368.7 |
-6368.7 |
Pretreatment |
0 |
-62.0 |
Hydrolysis |
0 |
-246.4 |
Centrifuges |
-380.9 |
-599.6 |
Pumps |
-1389.8 |
-1055.9 |
Back pressure turbine |
+32106.7 |
+49863.9 |
Condensing turbine |
+48051.6 |
0 |
Total |
+72019 |
+41531.3 |
Economic analysis
Ethanol and electric energy average seasonality over the period 2003-2012
Month |
Ethanol (%) |
Electric energy (spot market) (%) |
---|---|---|
January |
11.19% |
22.97% |
February |
7.64% |
-24.71% |
March |
9.29% |
-27.39% |
April |
5.76% |
-31.52% |
May |
-8.90% |
-26.25% |
June |
-12.61% |
-16.08% |
July |
-8.79% |
-5.77% |
August |
-6.53% |
-11.77% |
September |
-5.37% |
20.39% |
October |
-1.11% |
40.86% |
November |
2.81% |
41.92% |
December |
6.60% |
17.36% |
Investment costs by sector of the biorefinery, internal rate of return and net present value
Sector |
Cost (106 USD) |
||
---|---|---|---|
BioEE |
BioEth |
Flex |
|
Sugarcane reception, preparation and milling |
38.5 |
38.5 |
38.5 |
Combined heat and power plant |
50.2 |
42.9 |
50.2 |
Fermentation, distillation and tankage |
30.8 |
35.4 |
35.4 |
Sugarcane juice treatment |
23.1 |
23.1 |
23.1 |
Piping, general tankage and valves |
15.4 |
15.4 |
15.4 |
Licenses, project and ground leveling |
7.7 |
7.7 |
7.7 |
2G (pre-treatment, hydrolysis and C5 fermentation) |
0 |
9.6 |
9.6 |
Total |
165.8 |
172.7 |
180.0 |
IRR * |
7.6% |
8.3% |
8.0% |
NPV (10 6 USD) * |
-34.5 |
-30.0 |
-41.8 |
Chosen option between electric energy surplus (EE) and 2G ethanol production (2G) for the flexible biorefinery
Month |
1st to 8th year |
9th to 13th year |
14th to 25th year |
---|---|---|---|
January |
2G |
2G |
2G |
February |
2G |
2G |
2G |
March |
2G |
2G |
2G |
April |
2G |
2G |
2G |
May |
2G |
2G |
2G |
June |
2G |
2G |
2G |
July |
2G |
2G |
2G |
August |
2G |
2G |
2G |
September |
EE |
2G |
2G |
October |
EE |
EE |
2G |
November |
EE |
2G |
2G |
December |
2G |
2G |
2G |
The results of the economic analysis are presented in Table 7. Both IRR and Net Present Value (NPV) showed similar results, with BioEth being the best option, followed by the flexible biorefinery. As it can be seen, none of the options presented a positive NPV or, equivalently, an IRR higher than the Minimum Acceptable Rate of Return (MARR), assumed to be 11%/yr, when the present market prices for ethanol and electric energy in Brazil are considered. Nevertheless, as it will be shown later in the sensitivity analysis, an increase in ethanol price of 21.1% can turn all options feasible. Besides, specifically for the BioEth biorefinery, an increase of only 11.5% in this price would assure feasibility.
Unfortunately, a direct comparison of the obtained result with the ones from literature is not a straightforward task. There is a large variability in the economic premisses and in the technical solutions for the biorefineries that can be considered in a techno-economic study. For example, Seabra and Macedo (2011) [9] considered a 2G biorefinery adjacent to the 1G industrial plant (i.e., not sharing utilities and equipment, just importing bagasse), while Dias et al. (2011) [10] and Macrelli et al. (2012) [11] considered that 1G and 2G production plants were integrated (in different degrees). Even when similar processes are considered, the results can be quite different: while the autonomous 1G industrial plant in Dias et al. (2011) [10] obtained an IRR of 15.9 %, in Macrelli et al. (2012) [11] a similar plant obtained an IRR of 32.1 %.
Sensitivity analysis
Since ethanol prices presented an approximately normal distribution, its standard deviation was calculated and a variation equivalent to one standard deviation (20.5%) was used for the sensitivity analysis. On the other hand, electric energy price (spot market) did not present a normal distribution and its influence was better seen when the double of its current price was considered. Therefore, for this case a variation of 40% was considered and, for the other ones that had only punctual data available, a variation of 20% was chosen, thus assuming a percent variation similar to the one in ethanol prices. For Flex sensitivity analysis, the variations described were applied before the simulation of the seasonality effect on the prices.

Impact of electric energy selling prices (annual auctions) on the internal rate of return. All other prices kept unchanged.

Impact of electric energy selling prices (spot market) on the internal rate of return. The central point corresponds to a price (80.2 USD/MWh) equal to twice the current value. All other prices kept unchanged.
It is worth noticing that while Flex could reproduce almost perfectly the behaviour of BioEth (except for the higher investment cost), the same was not true for BioEE. This is due to the fact that the latter sold all its available electric energy in the auction market, which pays higher prices (in general), while the flexible biorefinery would not do this.

Impact of enzyme costs on the internal rate of return. All other prices kept unchanged.

Impact of ethanol selling prices on the internal rate of return. In (a), the current spot energy price (40.1 USD/MWh) is considered, while in (b) a spot energy price of twice this value (80.2 USD/MWh) is used. All other prices kept unchanged.
The non-linear behaviour of the system becomes evident in Figure 6. This is mostly caused by the fact that both tax rates and dividends only apply when there is profit. Therefore, the positive influence of an increase in ethanol prices on the IRR is attenuated by both of them and the second derivative of these curves is negative.

Impact of the investment cost on second generation ethanol on the internal rate of return. All other prices kept unchanged.
It is worth highlighting that the 2G process is coupled to the 1G process, which is responsible for the low investment cost of the former, when compared to literature [15], because costs of fermentation, distillation and combined heat and power stages are included in our 1G cost, which is scaled proportionally to the combined process flows.
Conclusions
A flexible sugarcane biorefinery (Flex) was simulated and compared to dedicated first generation + cogeneration (BioEE) and first + second generation ethanol (BioEth) biorefineries. The flexible one presented an inferior economic performance in all cases for 2012 market prices. Nevertheless, if an increase in electric energy prices in the spot market were considered, the flexible biorefinery could be the best option.
In general, all biorefineries were not economically feasible for 2012 selling prices and costs. This conclusion was actually validated in practice by recent governmental actions (April/2013) which aimed to improve the competitiveness of the ethanol industry. Additionally, of all parameters considered in the sensitivity analysis, ethanol prices were the only ones that could make the biorefineries economically viable, within the studied range of values. In fact, an increase in ethanol price of 21.1% would be sufficient to make feasible all biorefineries. Particularly for BioEth, a 11.5% increase in ethanol prices would be enough for viability.
Enzyme prices, on the other hand, were less significant than it could be expected. This is due to the fact that 2G ethanol costs were diluted by 1G ethanol’s, produced in higher volumetric rates. Therefore, the overall ethanol production cost in the integrated plant was not greatly influenced by enzyme prices.
Finally, it is obvious that the quantitative results presented here are dependent on the economic scenario proposed and on the assumed process yields and energy demands, but the presented methodology is general.
Methods
Process implemented
Main data for first generation ethanol production
Input |
Value |
Unit |
---|---|---|
Sugarcane flow |
500 |
tonne/h |
Sugarcane TRS (Total Reducing Sugars) |
15.86 |
% w/w |
Cleaning section |
||
Sugar losses |
1.5 |
% |
Cleaning efficiency |
70 |
% |
Water flow |
1 |
kg/kg of sugarcane |
Sugar extraction section |
||
Sugarcane bagasse humidity |
50 |
% w/w |
Sugar recovery (first mill) |
70 |
% |
Sugar recovery (total) |
96 |
% |
Duty |
16 |
kWh/tonne of fiber |
Water flow |
30 |
% w/w |
Sugarcane juice treatment section |
||
CaO flow |
2 |
kg/tonne of juice |
CaO concentration |
10 |
% w/w |
Heating final temperature |
105 |
°C |
Steam used |
53698 |
kg/h |
Water losses in flash |
6495.5 |
kg/h |
Polymer |
3534 |
kg/h |
Polymer concentration |
0.05 |
% w/w |
Sugar losses (decanter) |
6.8 |
% |
Sludge humidity |
50 |
% w/w |
Clarifier temperature (after decanter) |
92 |
°C |
Sugar losses (filter) |
5.6 |
% |
Filter cake humidity |
70 |
% w/w |
Water flow (filter) |
116 |
% |
Sugarcane juice concentration section |
||
Evaporators area |
8000 |
m2 |
Outlet sugar concentration |
21.4 |
% w/w |
Steam consumption |
190584 |
kg/h |
Steam produced |
181657 |
kg/h |
Pressure of steam produced |
2.5 |
bar |
Fermentation section |
||
Fermentation yield |
89 |
% |
Yeast concentration (wine) |
14 |
% w/w |
Wine ethanol concentration |
9 |
°GL |
Yeast concentration (after separation) |
70 |
% w/w |
Ration of yeast rich stream / sugar solution |
33 |
% w/w |
Ethanol purification section |
||
Specific steam consumption (1G) |
2.7 |
kg/L of ethanol |
Specific ethanol production (1G) |
91.6 |
L/tonne of sugarcane |
Specific vinasse + phlegm production (1G) |
10.1 |
kg/L of ethanol |
Main data for the cogeneration system
Parameter |
Value |
Unit |
---|---|---|
Cellulose LHVa |
15997.1 |
kJ/kg |
Hemicellulose LHVa |
16443.3 |
kJ/kg |
Lignin LHV a |
24170 |
kJ/kg |
Boiler outlet vapor pressure |
65.7 |
bar |
Boiler outlet vapor temperature |
520 |
°C |
Boiler efficiency |
92 |
% |
Back-pressure turbine outlet pressure |
2.5 |
bar |
Back-pressure turbine efficiency |
68 |
% |
Condensing turbine efficiency |
70 |
% |
Main data for second generation ethanol production
Main data used in the simulation |
Value |
Unit |
---|---|---|
Pretreatment |
||
Pressure |
2 |
Bar |
Temperature |
121 |
°C |
Cellulose to glucose conversion |
8.0 |
% |
Hemicellulose to xylose conversion |
74.0 |
% |
Solid/liquid ratio |
0.2 |
|
Acid solution concentration |
3 |
wt% |
Volumetric power (mixing)a |
342 |
W/m3 |
Space-time |
40 |
min |
Reactor volume |
182 |
m3 |
Pre-hydrolysis |
||
Cellulose to glucose yield |
20 |
% |
Solid/liquid ratio |
0.2 |
|
Enzyme/Cellulose ratio |
67.34 (20) |
g/kg (FPU/g) |
Space-time |
18 |
h |
Temperature |
50 |
°C |
Hydrolysis |
||
Cellulose to glucose yield |
65 |
%, w/w |
Solid/liquid ratio |
0.178 |
|
Volumetric power (mixing) a |
302.5 |
W/m3 |
Enzyme/Cellulose ratio |
67.34 (20) |
g/kg (FPU/g) |
Space-time |
54 |
h |
Temperature |
50 |
°C |
C5 Fermentation |
||
Xylose to ethanol yield |
70 |
%, w/w |
Temperature |
30 |
°C |
Space-time |
9 |
h |
EMSO Software
EMSO [13] was the software chosen as the platform for the simulations in this study. It is an equation-oriented, general purpose process simulator with its own modelling language [21]. Besides the several models for the main process pieces of equipments, the software also allows the user to implement his/hers own models. The software has several numeric solvers for solution of algebraic and differential-algebraic systems, and users can plug in their own numerical routines (in C/C++ or FORTRAN). Physical and thermodynamic properties can be added to the package database by the user whenever needed.
Economic analysis
Economic data, base case used as reference
Process and economic data |
Value |
---|---|
Time usage |
80% |
Days of operation |
210 days/year |
Ethanol direct/indirect costs (1G) |
94.75 USD/m3 |
Sugarcane costs (1G) |
314.78 USD/m3 |
Ethanol production cost(2G, extra cost) |
290.1 USD/m3 |
Electric energy production cost |
38.9 USD/MWh |
Ethanol transportation cost |
28.9 USD/L |
Administrative and general costs |
1.1 USD/TC |
Ethanol selling price |
513.7 USD/m3 |
Electric energy selling price (public auction) |
69.2 USD/MWh |
Electric energy selling price (spot market) |
40.1 USD/MWh |
Enzymes |
1.68 USD/kg |
Depreciation |
10%(p.y.) |
Minimum acceptable rate of return |
11%(p.y.) |
Decrease in production cost due to learning curve* |
0.3(1)%(p.y.) |
Tax rate (income and social contributions) |
34% |
Abbreviations
- 1G:
-
First generation
- 2G:
-
Second generation
- BioEE:
-
First generation biorefinery using all sugarcane bagasse (and trash) to produce electricity in a Rankine cicle
- BioEth:
-
First generation biorefinery using sugarcane bagasse surplus to produce second generation ethanol
- EE:
-
Electric energy
- EMSO:
-
Environment for Modeling Simulation and Optimization
- Flex:
-
Flexible biorefinery capable of operating as both BioEE and BioEth
- IRR:
-
Internal Rate of Return
- MARR:
-
Minimum Acceptable Rate of Return
- NPV:
-
Net Present Value
- SIF:
-
Simultaneous Isomerization and Fermentation
- TB:
-
Tonne of bagasse
- TC:
-
Tonne of sugarcane.
Declarations
Acknowledgements
The authors would like to thank the FAPESP BIOEN Program and the Brazilian National Council for Scientific and Technological Development (CNPq) for the financial support. The authors would also like to thank Mr. Alonso Constante Escobar (Tino), Mr. Carlos Henrique Manfredi and Mr. Marcelo Nishida for all technical information about 1G ethanol production and electric energy selling auctions.
Authors’ original submitted files for images
Authors’ Affiliations
References
- Macedo IC, Seabra JEA, Silva JEAR: Green house gases emissions in the production and use of ethanol from sugarcane in Brazil: The 2005/2006 averages and a prediction for 2020. Biomass Bioenergy 2008,32: 582-595. 10.1016/j.biombioe.2007.12.006View Article
- Zanin GM, Santana CC, Bon EPS, Giordano RLC, Moraes FF, Andrietta SR, Neto CCC, Macedo IC, Fo DL, Ramos LP, Fontana J: Brazilian bioethanol program. Appl Biochem Biotechnol 2000, 84: 1147-1163.View Article
- National Association of Motor Vehicles (ANFAVEA): Brazilian automotive industry yearbook. Tech. rep., São Paulo, 2012
- Gnansounou E: Production and use of lignocellulosic bioethanol in Europe: Current situation and perspectives. Bioresour Technol 2010, 101: 4842-4850. 10.1016/j.biortech.2010.02.002View Article
- Hassuani SJ, Leal MRLV, Macedo IC: Biomass power generation: Sugarcane bagasse and trash. Piracicaba: United Nations Development Programme and Sugarcane Technology Centre; 2005.
- Electric Energy National Agency – ANEEL (in portuguese) http://www.aneel.gov.br
- Electric Energy Commercialization Chamber – CCEE (acronym in portuguese) http://www.ccee.org.br/
- Center of Advanced Studies in Applied Economy – CEPEA/ESALQ/USP (in portuguese) http://www.cepea.esalq.usp.br
- Seabra JE, Macedo IC: Comparative analysis for power generation and ethanol production from sugarcane residual biomass in Brazil. Energy Policy 2011, 39: 421-428. http://www.sciencedirect.com/science/article/pii/S0301421510007706 10.1016/j.enpol.2010.10.019View Article
- Dias MO, Cunha MP, Jesus CD, Rocha GJ, Pradella JGC, Rossell CE, Maciel Filho R, Bonomi A: Second generation ethanol in Brazil: Can it compete with electricity production? Bioresour Technol 2011,102(19):8964-8971. 10.1016/j.biortech.2011.06.098View Article
- Macrelli S, Mogensen J, Zacchi G, et al.: Techno-economic evaluation of 2 nd generation bioethanol production from sugar cane bagasse and leaves integrated with the sugar-based ethanol process.Biotechnol Biofuels 2012, 5: 22. 10.1186/1754-6834-5-22View Article
- Dias M, Junqueira T, Cavalett O, Cunha MP, Jesus C, Rossell C, Filho R, Bonomi A: Integrated versus stand-alone second generation ethanol production from sugarcane bagasse and trash. Bioresour Technol 2012,103: 152-161. 10.1016/j.biortech.2011.09.120View Article
- Soares RP, Secchi AR: EMSO: A new environment for modelling, simulation and optimisation. Comput Aided Chem Eng 2003, 14: 947-952.View Article
- Agblevor F, Rejai B, Wang D, Wiselogel A, Chum H: blueInfluence of storage conditions on the production of hydrocarbons from herbaceous biomass. Biomass Bioenergy 1994, 7: 213-222. 10.1016/0961-9534(94)00063-YView Article
- Eggeman T, Elander RT: Process and economic analysis of pretreatment technologies. Bioresource Technol2005,96(18):2019-2025. 10.1016/j.biortech.2005.01.017View Article
- Furlan FF, Costa CBB, Fonseca GC, Soares RP, Secchi AR, Cruz AJG, Giordano RC: Assessing the production of first and second generation bioethanol from sugarcane through the integration of global optimization and process detailed modeling. Comput Chem Eng 2012, 43: 1-9.View Article
- Canilha L, Chandel AK, Suzane dos Santos Milessi T, Antunes FAF, Luiz da Costa Freitas W, das Graças Almeida Felipe M, da Silva SS: Bioconversion of sugarcane biomass into ethanol: An overview about composition, pretreatment methods, detoxification of hydrolysates, enzymatic saccharification, and ethanol fermentation. J Biomed Biotechnol 2012, 2012: 1-15.View Article
- Wooley R, Putsche V: Development of an ASPEN PLUS physical property database for biofuels components. NREL, Tech. rep., Report MP-425-20685 1996, 38
- Silva C, Zangirolami T, Rodrigues J, Matugi K, Giordano R, Giordano R: An innovative biocatalyst for production of ethanol from xylose in a continuous bioreactor. Enzyme Microb Technol 2012, 50: 35-42. 10.1016/j.enzmictec.2011.09.005View Article
- Pereira LTC, Pereira LTC, Teixeira RSS, Bon EPS, Freitas SP: Sugarcane bagasse enzymatic hydrolysis: rheological data as criteria for impeller selection. J Ind Microbiol Biotechnol 2011,38(8):901-907. 10.1007/s10295-010-0857-8View Article
- Rodrigues R, Soares RP, Secchi AR: Teaching chemical reaction engineering using EMSO simulator. Comput Appl Eng Educ 2010,18(4):607-618. 10.1002/cae.20255View Article
Copyright
This article is published under license to BioMed Central Ltd. This is an Open Access article distributed under the terms of the Creative Commons Attribution License (http://creativecommons.org/licenses/by/2.0), which permits unrestricted use, distribution, and reproduction in any medium, provided the original work is properly cited.