![]() |
Xiamen Bioleader Environmental Protection Co., LtdProfessional Supplier of Biodegradable Tableware and Food Packaging! |
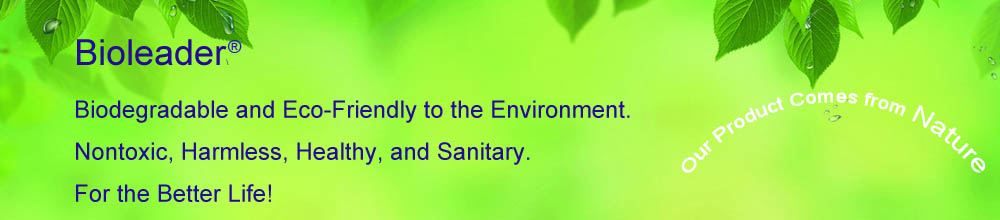
Why Sugarcane Bagasse is the Most Promising Pathway for Cellulosic Ethanol
This article was originally published in Digest content partner site Energy Trends Insider, a free newsletter by Consumer Energy Report, which is geared toward financial and investment issues in the energy industry.
The history of cellulosic ethanol is a lot longer than most people probably realize. In 1819, French chemist Henri Braconnot discovered how to break cellulose down into component sugars by treating biomass with sulfuric acid. Once sugars are released from cellulose, the solution can be fermented to ethanol in processes that are very similar to those used to produce corn ethanol or sugar cane ethanol. Regardless of the way the sugars are released, processes that produce ethanol from cellulosic sugars are collectively categorized as cellulosic ethanol.
The Germans first commercialized cellulosic ethanol production from wood in 1898. The technology was commercialized in the U.S. in 1910, when Standard Alcohol Company built a cellulosic ethanol plant in South Carolina to convert lumber mill waste into ethanol. Standard Alcohol later built a second plant in Louisiana. Each plant was capable of producing over 5,000 gallons of ethanol per day from wood waste, and both were in production for several years before being idled for economic reasons.
Many subsequent attempts were made to commercialize cellulosic ethanol during the 20th Century, but there were huge challenges in developing
cellulosic ethanol as a cost-competitive energy option. Because of the extra steps involved relative to corn or sugarcane ethanol, capital and operating costs are higher for cellulosic ethanol than for ethanol derived from carbohydrates. But the ongoing attraction of cellulosic ethanol is the potential to utilize waste streams that are cheap or even negatively priced to produce the ethanol. Therefore a number of companies continue to work toward commercialization.
I have long felt that the residue from the processing of sugarcane — bagasse — seems to be the lowest hanging fruit for the production of cellulosic ethanol (better even than municipal solid waste). There are residual sugars in the bagasse, and it is washed, pulverized, and already delivered to a factory. In fact, even after using some bagasse to power their plants, sugar plants struggle to dispose of excess bagasse. Thus, the economics of bagasse versus purpose-grown crops for cellulosic ethanol production should be significantly better.
Some companies have focused on the potential of bagasse for ethanol production. In 2008 Verenium announced their intention to build a bagasse-based ethanol demonstration plant in Louisiana and a commercial plant in Florida. Those plans ultimately did not pan out, and Verenium sold their cellulosic ethanol business to BP.
But Blue Sugars Corporation (previously KL Energy) recently reported that they had achieved the major milestone of claiming the first cellulosic ethanol tax credits under the RFS2 for a 20,000 gallon batch of cellulosic ethanol produced from bagasse. This is presumably the 20,069 gallons of cellulosic biofuel that the EPA lists for April. (No cellulosic biofuel production was reported in May or June).
Cellulosic ethanol commercialization still faces a number of challenges. Capital and operating costs are expected to remain higher than for corn ethanol producers, and even they are currently struggling with low margins. The ethanol market also faces the hurdle of the blend wall, which makes it difficult to expand domestic production without increases in E15 and E85 consumption, and/or ethanol exports.
Nevertheless, I believe that those focused on waste feedstocks have the greatest chance of successful commercialization of cellulosic ethanol. I would put my money on bagasse as the most attractive feedstock, followed by municipal solid waste and agricultural residues.
Beyond ethanol, Solazyme has reported production of algal fuel from sugars derived from bagasse.